It's a Maintenance Marathon!
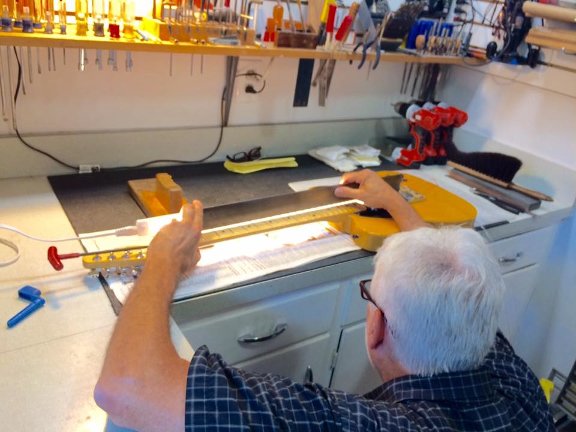
Kenny at the bench. Image courtesy Kepone Cowboys.
06/23/2022
I've let some of my guitar maintenance pile up, so I have a group of guitars that need to visit my friend and excellent luthier/tech, Kenny Marshall, who does all my work. Around 1994 there came a time in my life when I no longer wanted to wield sharp objects around my expensive instruments. Most of them were being used for sessions, where I needed a really good setup job done. That's when I was directed to Kenny by my studio player friends. When Kenny does a setup it goes far beyond cutting nut slots. If the guitar needs the frets leveled and crowned to get the action down, he'll do that. If it needs the fret ends rounded, he'll do that, plus file the bridge for intonation if necessary. On the electrics he also sets up the pickups. I found that he was capable of far better work than I am. When you need the best, go to the best. As a result, I have become... um, spoiled. So, for the current exedition I've rounded up the guitars and put a set of new strings in each case. I'm going to invite you to come along on my journey and see what happens. Here are the candidates:
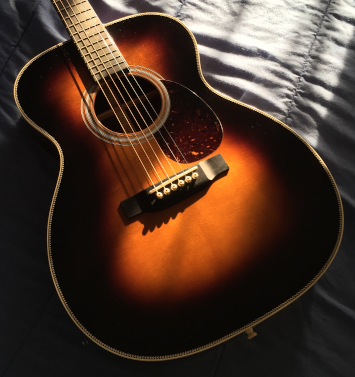
2021 Martin OM-28 Standard Reimagined. My lovely, supportive wife gave this great guitar to me to celebrate my fortieth year in the recording industry. She also suggested I take it to Kenny to get his initial set up so it would play right for me. Though it was set up pretty well at the factory with a Plek machine, my feeling was that the nut was a tad high. It was close, but no cigar.
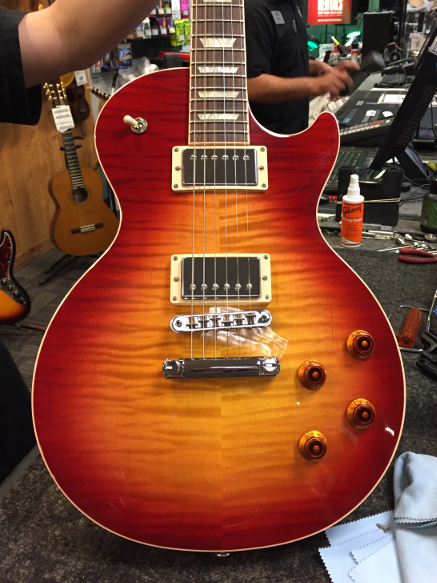
2018 Gibson Les Paul Standard T ("Traditional"). Gibson did their premium Plek job on this guitar but again the nut seems a tad high for me. Also, even though the frets are pretty tall, it doesn't feel as secure as it could in bends, not nearly as secure as my other Gibson guitars that Kenny has set up. It also has the classic Gibson tuning problem, ie., the strings bind in the nut slots. After a good bend on the upper strings, the guitar seems to return off-pitch. I've used it on some sessions but I'm a little uncomfortable with the tuning and bending issues. While he's in there I'm going to get Kenny to install the toggle switch "poker chip."
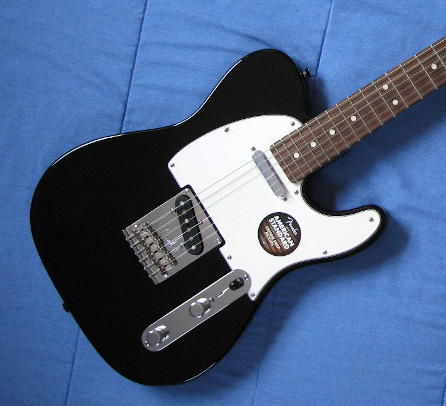
2013 Fender American Standard Telecaster. The guitar came with a pretty good setup from the factory, but it has come into high demand in my studio work and I want it optimized. When you realize that the guitar's 25.5" scale isn't native to me, you can bet that I want it to be as comfortable as is possible. Meanwhile, even though I have set the intonation in a rudimentary way, I've still been spending an inordinate amount of care bending within chords to pull those chords into tune.
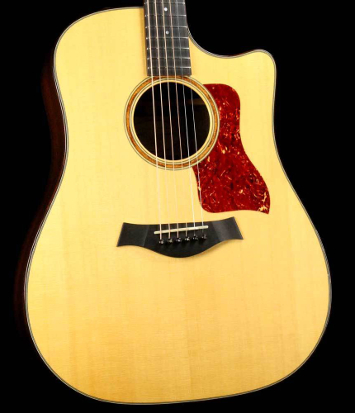
2004 Taylor 710ce. This is a truly new-old-stock 2004 guitar without a scratch on it that I bought in 2019. The action is relatively high at both bridge and nut. It feels a bit... clumsy, and the high action takes a lot of the fun out of playing the instrument. I have no idea whether fret work or even a neck reset will be required to bring the action down.
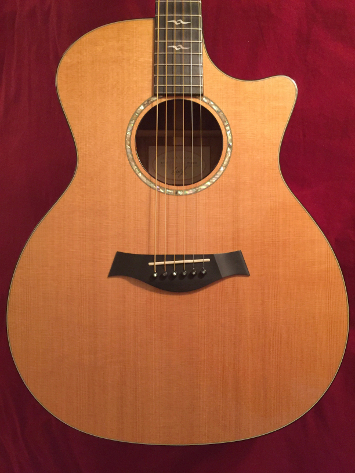
1999 Taylor K14c. This is the silver tuna! It was purchased for me by my lovely wife in 2000 to commemorate our twentieth anniversary and set up by Kenny back then. The guitar's production was started on the last day of production before Taylor's Christmas break in 1999. I've played it during the intervening twenty years and its frets are getting pretty low. Time for a re-fret? Probably. Kenny has referred me to the Jescar site to consider fret sizes and I'm trying to figure things out. Will it be stainless or nickel silver? He says Taylor's ebony fingerboards tend to be pretty dry so it will want extra care as he works.
On his business card Kenny calls himself a "playability specialist." He is popular with professional clients and has a constant stream of work coming in from clients in Nashville and other out-of-state locations. He has a professional resume' a mile long with some really impressive names and as a result, he has a backlog of work all the time. I love to watch Kenny do an assessment because he just exudes experience and casual competence. He serves some large bands and orchestras that have a deal with him where they can save money by being willing to drop off a group of instruments for repairs and wait, sometimes for months, for him to return them. That allows him to insert those instruments into any slack times and keep his income stream constant. With the current workload, he said that if I waited a bit, we could set a date when he expected to catch up reasonably well and we could insert my bunch into the work stream without him holding onto them. So, we arranged an appointment a few weeks later. At the appointed time, my wife and I traveled to the town where he has his bench. After catching up on our lives, we spent two and a half hours looking at the instruments. Once Kenny figured out what was needed and gave us an estimate, we left the instruments with him. A couple of notes from the consultation are memorable:
On the Taylor 710ce: This one was a little complicated, and I'm not surprised. Once Kenny set the relief into the ballpark of his goal, the G string was lying right down on the first fret because its slot was cut too deep. At first he scratched his head and said he could fill with nut material and superglue and recut the slot and I said that was fine with me. However, there turned out to be two high spots in the frets, one above the twelfth and another right at the top fret on the board. He'll be dealing with those. Between the target relief change and reducing the high spots, he thought the action would come down enough at the center that it would probably be best to cut a new nut and saddle. He anticipated a lot of work on this one and his estimate for its setup was higher than those of the others.
On the Taylor K14c: Yep, the frets are down to around thirty-one thousandths after twenty-two years. We discussed fret wire sizes and settled on .043h x .080w, not much different from vintage spec. There is a high spot in the fingerboard and he'll need to take care of it before re-fretting. With the higher frets he'll be cutting a new nut and bridge. While looking at it he played it a bit, grinned, and said, "I have NEVER heard a Taylor sound this good. I bet it didn't sound this good when you bought it." Uh, no, it didn't. I had begun to think it was a pretty extraordinary guitar and this was a nice reinforcement to my impression. I'm taking a chance and going with stainless frets. Yes, I know that some consider them bright. With a sly grin, Kenny said, "If you don't like the stainless I can always buy the guitar from you!"
So, it is a maintenance marathon. I will be fascinated to see what Kenny thinks of the guitars and what work will be needed. I will report after the consultation.
******
A couple of weeks have elapsed and most of the results are in! The K14c still needs some work, so I will be going back for it in a few weeks. However, I did pick up the rest of the guitars from Kenny and I've had a week to try them out. As always, once a tech dives into a guitar there's usually unexpected stuff to contend with. I let Kenny choose the order to bring the guitars out. Here are the results on the four guitars he finished:
Kenny proudly brought out the NOS 2004 Taylor 710ce first. I didn't want to say it, but before he started working, the action was a bit of a basket case, way too tall to be comfortable for me and not at all consistent. There were lots of little issues with it. Firstly, Kenny had to work a hump out of the neck. As usual, the treble and bass sides didn't respond to the truss rod at the same rate, so he had to work with it a bit. Secondly, frets two and three were low. He had to reset them to bring them UP to the level of the rest. Once that was accomplished, he had to dress frets eight through thirteen to bring them into line with the rest of the frets. And then he had to deal with the last fret, number twenty, where the fingerboard turned up a little bit. The guitar had arrived to me with an extra tall nut; and further, a shim had been placed under the saddle to give clearance over the hump. Kenny cut a new nut and saddle and improved the intonation with a different saddle profile. He rounded the fret ends as well to make them more comfortable. Results: Dramatic! Wonderful. I picked it up and played and immediately exclaimed, "OH YEAH!!!" Despite being a big dread, this guitar is now easy and comfortable to play. The "cheese slicer" high E is now low and comfortable and the height of the G is now equalized with the rest of the strings. Hammer-ons and pull-offs are much more comfortable. I can play fingerstyle on it easily and then turn and lean into it with strumming as well. This guitar was easily the most improved of the lot and I can see why Kenny pulled it out first. The week after I picked it up I took it right into the studio and it performed marvelously.
Next came the 2021 Martin OM-28. The first issue was leveling a neck hump between frets eleven and fifteen. That was followed by addressing a fret high on the neck that stood a tad high and had to be reset lower. Finally, the fret ends needed to be dressed. Though the guitar came from the factory with a pretty good action, the result was an exceptional action. This guitar with its intimate tone is now made even more intimate by virtue of the comfortable feel of the neck that Kenny gave it.
Next, Kenny brought out the 2013 Fender Telecaster. He said that it primarily needed a bunch of fret dressing but he also adjusted the intonation and rounded the fret ends with his twelve-cut method. To top things off he used 0000 steel wool to restore the matte finish on the back of the neck where nine years of playing had polished it smooth. A tiny bit of rounding to the fingerboard edges resulted from his work on the fret ends but nothing drastic. Voile'! It is much more pleasant to play. I don't have to constantly use body English to drag the strings into tune within chords because of the improved intonation. Chimey chording sounds great. I also used this guitar in the studio the week after I picked it up and it was comfortable and sounded great.
And finally there was the 2018 Gibson Les Paul Standard. Even before I bought it, I knew it would need Kenny's loving touch. However, COVID had prevented me from taking it to him. Frets one and two were low and had to be brought up. Frets seven, fifteen, and eighteen were high and had to be lowered. Kenny re-cut the nut slots as was necessary for the guitar to keep tune without binding. He intonated the guitar and leveled the stop bar tailpiece to equalize the tension feel of the strings as contributed by bridge break angle as well. The result was a superb setup, much more secure in bends while being low, consistent, and level throughout. It plays far more in tune than it did. I've been playing it for several days now and have found that it holds tuning extremely well, even when subjected to extreme bending. The guitar also feels much more secure in bends throughout the neck. The change in the guitar is probably second only to the 710ce. This Les Paul has ended up a "no-reservations" instrument - I can feel right at home on it and don't have to think about how to approach it. While he was working, I had Kenny install the 'poker chip" pickup selector switch washer that was delivered in the case. There was a pickguard delivered in the case as well, but I've chosen to leave it off for now to reveal the lovely maple figure.
Well, there you go. Kenny was able to improve each of these instruments, right across the board, and at least two of them dramatically. It is interesting to me that the two that had been set up with the Plek machine were capable of such improvement. I am already enjoying the results of Kenny's work in the studio. I guess the rest is up to me!
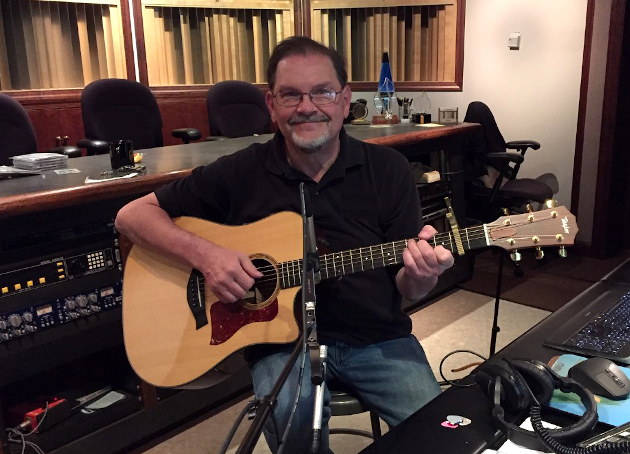
And now the rest of the story can be told, how the Taylor K14c became a "prodigal guitar." More, HERE.
=
=